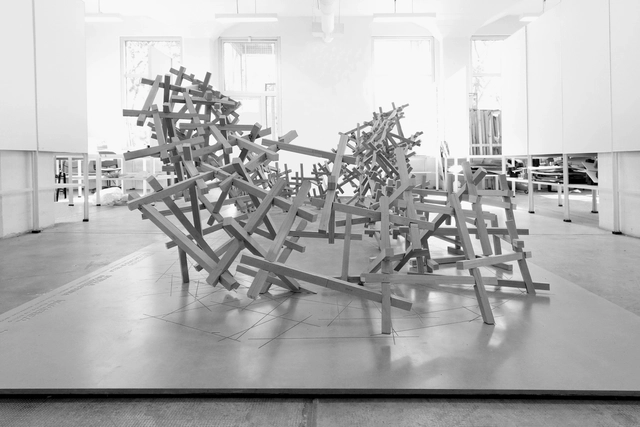
En el marco de un curso de arquitectura de la Universidad Torcuato Di Tella, nace el Pabellón Ditebius Torus. Esta creación indaga sobre las estructuras recíprocas en madera, utilizando herramientas de diseño y fabricación digital.
El taller, encabezado por el arquitecto Matias Imbern, se orienta a la exploración del diseño y la fabricación digital, entendiendo el creciente progreso de los medios digitales como un generador de nuevas posibilidades de proyectos. El objetivo principal del curso recae en el desarrollo de habilidades y técnicas de diseño aplicado a los procesos digitales, enfatizando la relación entre computación y procedimiento.
Ditebius Torus fue posible gracias a la colaboración de Masisa, el ayudante del taller, Eugenio Tenaglia y el grupo de invesitgación conformado por: Agustina García Campos, Felipe Ginevra, Agostina Giovo, Agustina González Morales, Gastón Hermida, Tomás Meneghetti, Victoria Nicolich, Agustina Suar, Magdalena Viegener, Gabriela Zarwanitzer y Martín Zemma.
Descripción del arquitecto. Mediante el análisis y la documentación rigurosa de casos de estudio se traza un perfil de investigación proyectual que profundiza en órdenes geométricos y técnicas materiales con el fin de brindar herramientas para el desarrollo de nuevos sistemas tectónicos. Es a partir de repensar los sistemas existentes, mediante la introducción de procesos digitales, que se busca optimizar rendimientos materiales y lógicas programáticas y/o formales tradicionales.
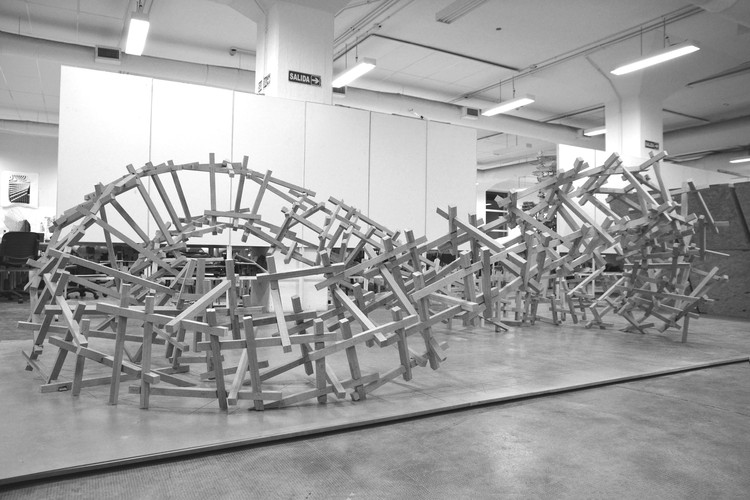
La construcción de modelos digitales de geometría asociada inicia el desarrollo del proyecto, constituyéndose en un instrumento para generar variaciones alternativas de estos sistemas. Esto da lugar a una fase de investigación proyectual, que otorga nuevas posibilidades innovativas, a partir de manipular interfaces entre modelos digitales y prototipos físicos.
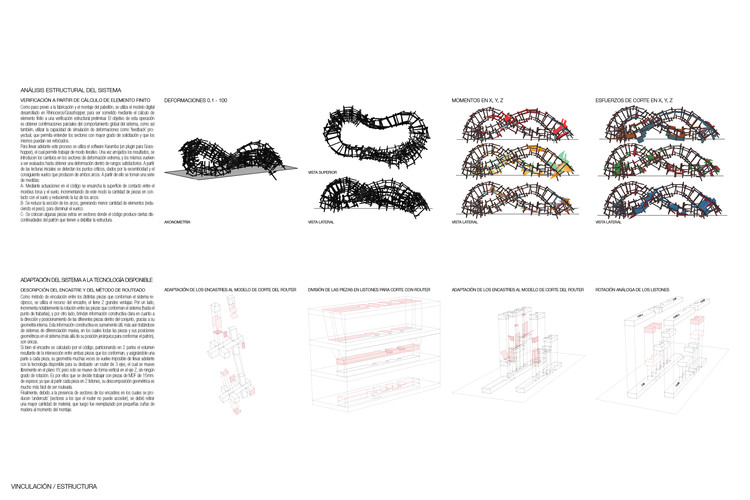
A través de la fabricación de prototipos, que combinen técnicas de fabricación digital con técnicas analógicas, los alumnos podrán explorar las nuevas facultades y potencialidades que ofrecen las herramientas digitales en arquitectura.
PATRÓN GENERATIVO
El sistema se desarrolla a partir de la investigación de estructuras recíprocas de madera, utilizando elementos de sección cuadrada y patrones geométricos combinados. Como estructura recíproca se entiende el desarrollo de un ensamblaje tridimensional de elementos que se apoyan mutuamente entre sí, con cierto coeficiente de rozamiento. Cada elemento se apoya en el siguiente y así sucesivamente hasta que el último se apoye en el primero, conformando así un sistema cerrado, autosustentado. Este tipo de estructuras tiene la capacidad de cubrir grandes luces con elementos pequeños, generando una estructura estable y versátil, sin necesidad de elementos agregados.
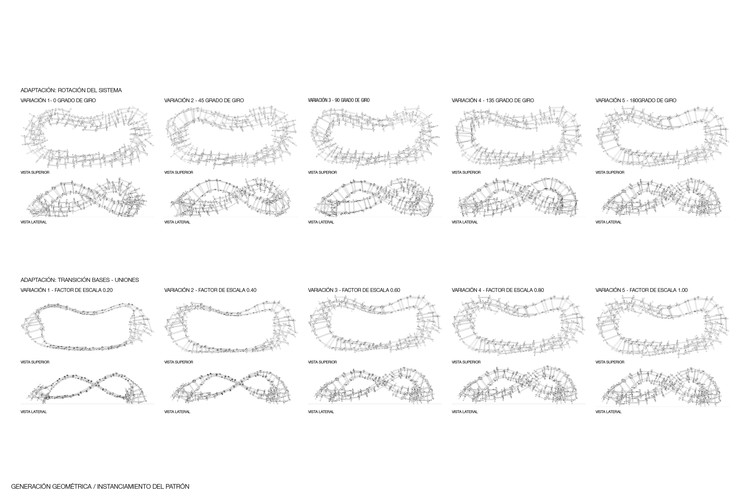
El sistema comienza con el desarrollo de un módulo bi-dimensional, combinando líneas tanto horizontales como verticales formando una grilla. Luego, para generar espesor e inercia, se configuran dos patrones en caras opuestas, incorporando piezas transversales que cosen ambas capas. Cada una de las líneas originales es subdividida y explotada según la cantidad de intersecciones con las líneas en sentido opuesto.
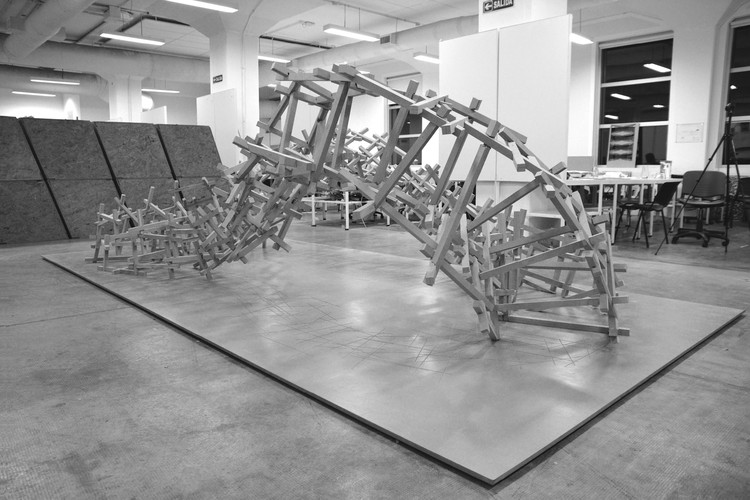
A partir de ello se generan la malla definitiva: en el desarrollo superior, en sentido horizontal, la misma está compuesto por una secuencia de tres verdaderos-nueve falsos en cada línea horizontal, desfasadas una de las otras, en sentido ascendente, tres módulos a la derecha. El orden vertical se conforma por un patrón de un verdadero-dos falsos, empezando en el inicio de cada línea horizontal. Respecto al orden inferior, en sentido horizontal, el mismo es igual al superior, y se encuentra desplazado cuatros módulos hacia la derecha. La secuencia vertical inferior difiere de la superior, compuesta por un patrón de cuatro verdaderos-tres falsos, desplazadas entre sí, de izquierda a derecha, un módulo hacia arriba. El mismo se intercala con el patrón en distintos momentos de la línea horizontal. Por último, las piezas transversales son las que cosen ambos patrones. Las uniones entre ambas capas se realiza siempre entre piezas verticales en sentido superior, y horizontales del lado inferior. Los mismos se ubican en las piezas horizontales, en el inicio del tercer módulo.
EL MÓDULO ADAPTABLE
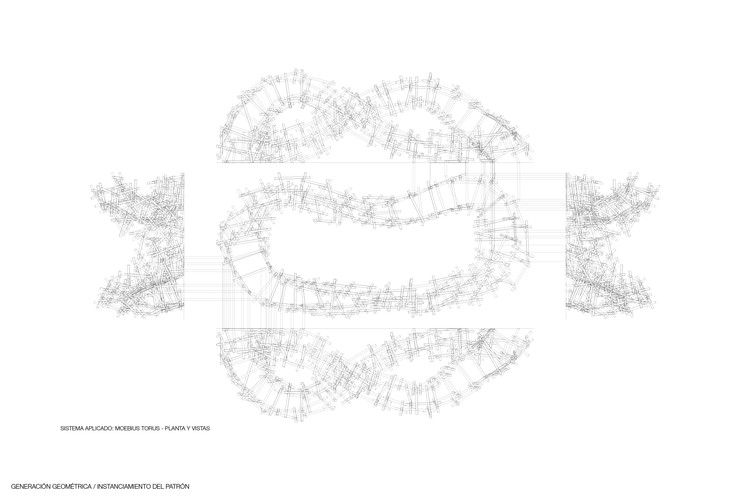
El sistema está formado por un módulo que se instancia reiteradas veces, en relación a las coordenadas rectoras de una superficie generatriz (U, V, W). Al mismo tiempo, el sistema es lo suficientemente versátil como para permitir su adaptabilidad a diversas curvaturas según distintos parámetros iniciales: curvas abiertas, curvas cerradas, superficies y volúmenes. De este modo, se genera un módulo capaz de adaptarse a una amplia gama de geometrías diversas, desde líneas abiertas (como condición genérica del sistema), hacia estructuras más elaboradas como superficies y volúmenes, que permiten la evolución del sistema a niveles más de mayor complejidad.
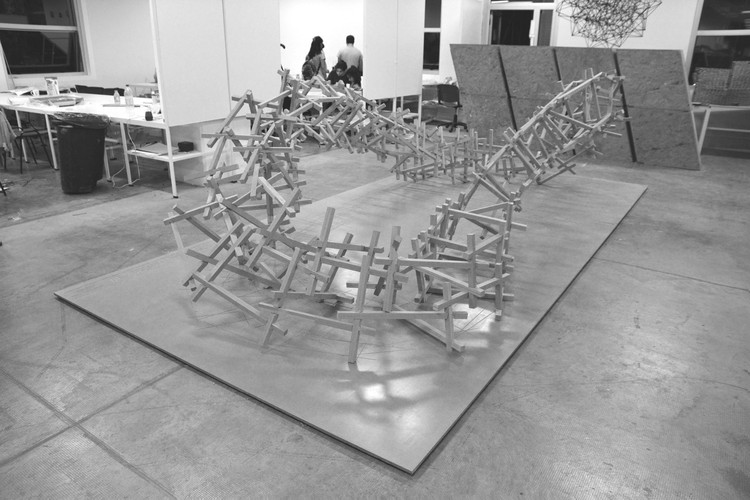
Para cada uno de estos estudios se analizan tres posibles diferenciaciones del sistema. Por un lado la subdivisión de la curva original e incorporación de polígonos en su centro para la aplicación del patrón, y por el otro, la rotación de los mismos, los cuales permiten manipular la perfomance del pabellón. La tercera diferenciación depende del contexto en el cual se implante, la transición entre bases y uniones como refuerzo estructural del sistema. Esto último es necesario para un control tridimensional del sistema, trabajando con madera, que permite generar sistemas que desafían constantemente las convencionalidades estructurales del material.
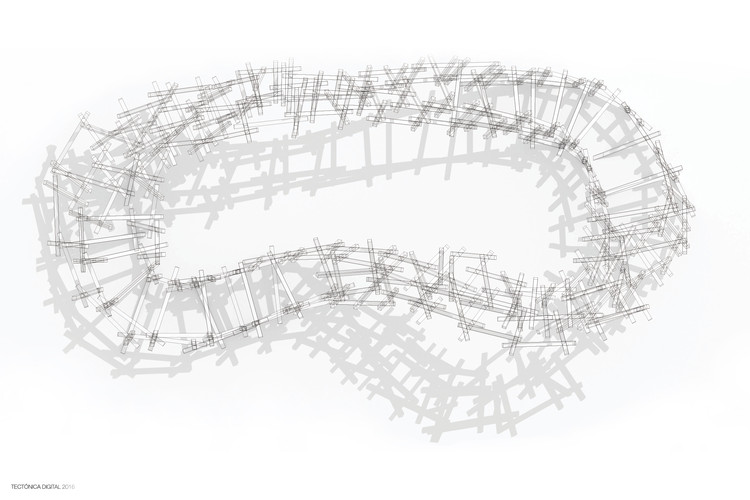
DESCRIPCIÓN DEL SISTEMA
El sistema es adaptado a una curva cerrada, generatriz de “moebius torus”. La curva original se subdivide y en cada subdivisión se ubica un polígono. A continuación, se introduce en la serie una rotación total que llega a completar los 360º, de tal forma que cada polígono se rota un cierto porcentaje dependiendo de la cantidad de subdivisiones, en pos de generar una continuidad superficial a lo largo de toda la geometría. Una vez que se instancia el patrón del módulo adaptable, el mismo rota naturalmente con el movimiento del moebius torus. En dos caras funcionan los elementos horizontales y verticales superiores e inferiores, opuestos entre sí. En las otras dos, se ubican las piezas transversales.
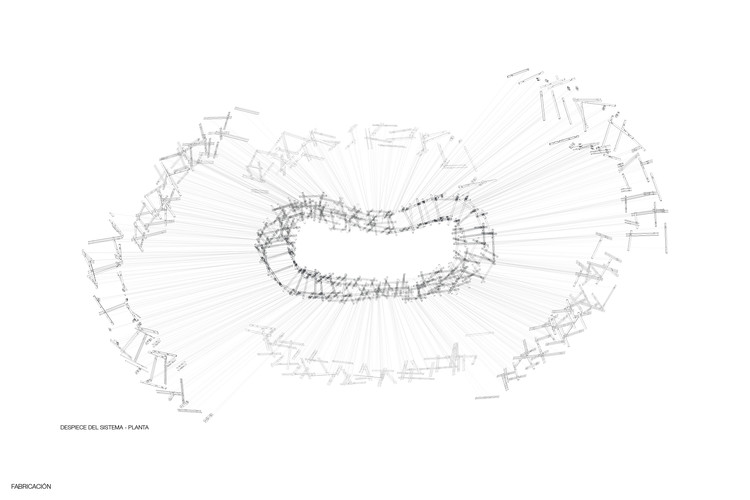
Cada variable de adaptabilidad: subdivisión de la curva inicial, rotación del sistema, y escala de bases y uniones es estudiada individualmente en cinco variantes, en busca de un balance entre performance y eficiencia estructural. La geometría final encuentra dos momentos de apoyo en las partes más bajas de su base, mientras el resto de la geometría aumenta en altura y excentricidad a medida que se aleja de los mismos. La escala de las bases y uniones significa el incremento de tamaño de los polígonos base y disminución de los polígonos de los arcos a medida que se aumenta la altura de la geometría global.
ANÁLISIS ESTRUCTURAL / CÁLCULO DE ELEMENTO FINITO
Como paso previo a la fabricación y el montaje del pabellón, se utiliza el modelo digital desarrollado en Rhinoceros/Grasshopper, para ser sometido mediante el cálculo de elemento finito a una verificación estructural preliminar. El objetivo de esta operación es obtener confirmaciones parciales del comportamiento global del sistema, como así también, utilizar la capacidad de simulación de deformaciones como ‘feedback’ proyectual, que permita entender los sectores con mayor grado de solicitación que deban ser reforzados. Para llevar adelante este proceso se utiliza el software Karamba (un plugin para Grasshopper), el cual permite trabajar de modo iterativo. Una vez arrojados los resultados, se introducen los cambios en los sectores de deformación extrema, y el sistema vuelve a ser evaluado hasta obtener una deformación dentro de rangos satisfactorios. En las lecturas iniciales se detectan los puntos críticos, dados por la excentricidad y el consiguiente vuelco que ambos arcos producen. A partir de ello se toman una serie de medidas:
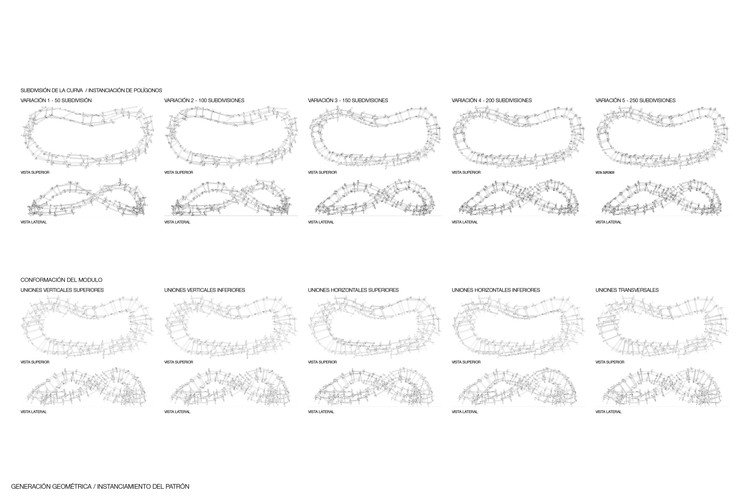
- Mediante actuaciones en el código se ensancha la superficie de contacto entre el moebius torus y el suelo, incrementando de este modo la cantidad de piezas en contacto con el suelo y reduciendo la luz de los arcos.
- Se reduce la sección de los arcos, generando menor cantidad de elementos (reduciendo el peso), para disminuir el vuelco.
- Se colocan algunas piezas extras en sectores donde el código produce ciertas discontinuidades del patrón debilitan la estructura.
ENCASTRE Y MÉTODO DE FREZADO
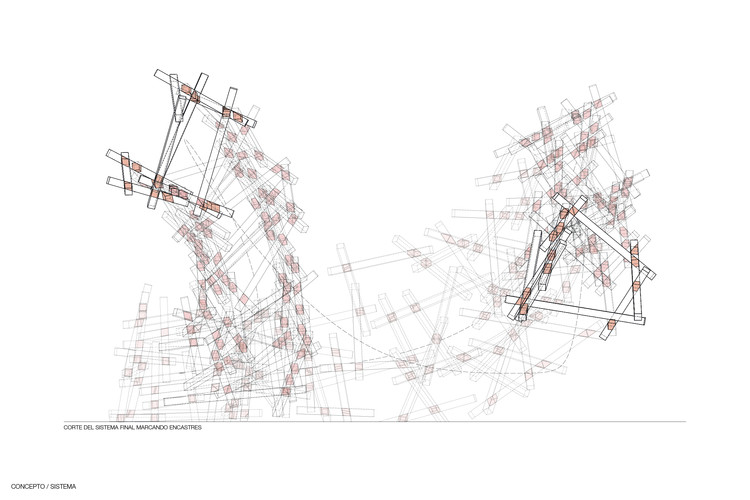
Como método de vinculación entre los distintas piezas que conforman el sistema recíproco, se utiliza el recurso del encastre, el tiene 2 grandes ventajas: Por un lado, incrementa notablemente el rango de rotación entre las piezas, y por otro lado, brindan información constructiva clara en cuanto a la dirección y posicionamiento de las diferentes piezas dentro del conjunto, gracias a su geometría interna. Esta información constructiva es sumamente útil, más aún tratándose de sistemas de diferenciación masiva, en los cuales todas las piezas y sus posiciones geométricas en el sistema (más allá de su posición jerárquica para conformar el patrón), son únicas.
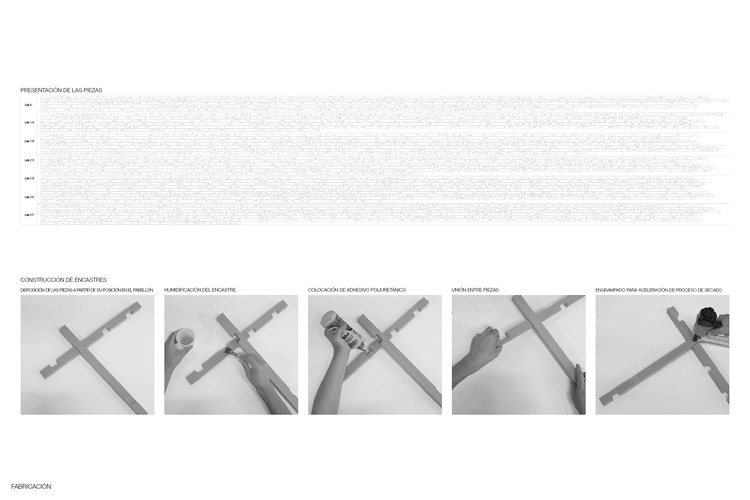
El encastre es calculado por el código, particionando en 2 partes el volumen resultante de la intersección entre ambas piezas que los conforman, y asignándole una parte a cada pieza. Sin embargo, su geometría muchas veces se vuelve imposible de llevar adelante con la tecnología disponible para su desbaste: un CNC router de 3 ejes, el cual se mueve libremente en el plano XY, pero solo se mueve de forma vertical en el eje Z, sin ningún grado de rotación. Es por ello que se decide trabajar con placas de MDF de 15mm. de espesor, ya que al partir cada pieza en 2 listones, su descomposición geométrica es mucho más fácil de ser frezada.
Finalmente, debido a la presencia de encastres en los cuales se producen ‘undercuts’ (sectores a los que el CNC router no puede acceder), se debió retirar una mayor cantidad de material, que luego fue reemplazado por pequeñas cuñas de madera al momento del montaje.
PROCESO DE FABRICACIÓN
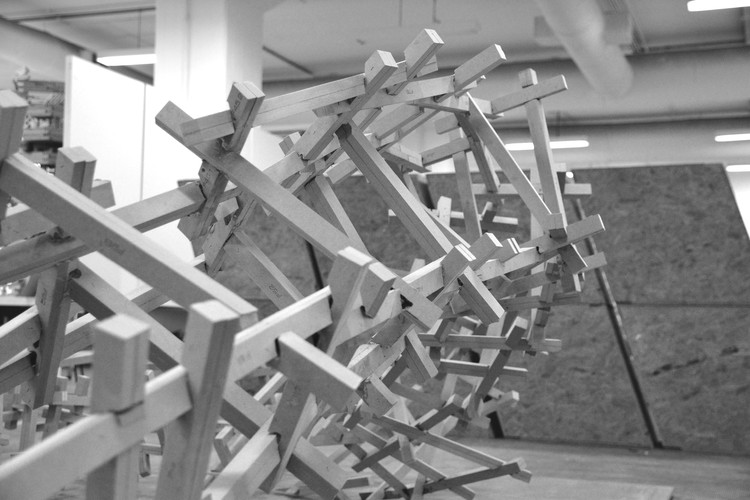
La fabricación digital de las piezas es la culminación de una serie de procesos digitales a través de los cuales se va refinando su geometría. Luego de ser instanciado el patrón en la trayectoria/superficie estipulada, se procede a realizar la intersección entre piezas. A continuación, se calculan los encastres, y cada piezas es dividida en 2 o más listones (dependiendo de la dirección en las que se dan los encastres) de 15mm. de espesor. A continuación, utilizando un software llamado RhinoNest, las piezas son colocadas de forma optimizada (de modo de producir el menor desperdicio material) dentro de las placas de MDF de 2,6x1.83m. La geometría se exporta hacia otro software, llamado AlphaCAM, el cual permite simular de forma digital el comportamiento del CNC router de forma previa al desbaste final. El frezado consiste en 3 procesos: el numerado de las piezas, el desbaste de los encastres y por último, el corte de cada listón. Para simplificar todo el proceso, el pabellón se dividió en 3 lotes de corte, los cuales están divididos cada uno, en 2 sublotes de montaje.
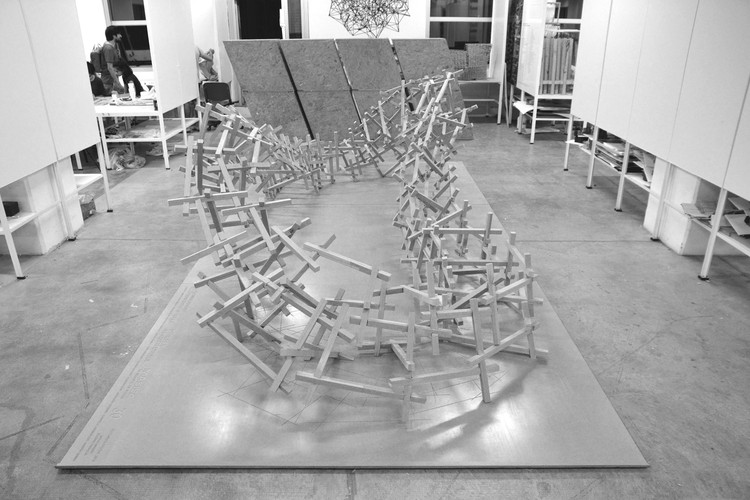
El proceso continúa luego de modo analógico, clasificando y seleccionando los listones de acuerdo a su numeración, encolándolos para conformar las piezas (utilizando grampas para acelerar el proceso de secado de la cola) y luego retirando el material de viruta excedente que deja el proceso de frezado.
Finalmente, para materializar el encastre se utiliza nuevamente el encolado y el engrampado de los mismos. Como ayuda para el montaje, se utiliza una serie de soportes que fueron frezados junto con las piezas, los cuales otorgan la altura y rotación de algunas piezas del pabellón, simplificando de éste modo tanto su precisión geométrica como su soporte a medida que se avanza con el montaje, hasta que el sistema esté completo y comience a funcionar la reciprocidad del mismo.